www.industriogteknik.com
18
'11
Written on Modified on
Produktion af glasbeholdere til farmaceutisk brug
SPAMI, der er en virksomhed i Stevanato Group, har udviklet et system til kvalitetskontrol af glasprodukter. Systemet anvender kontrol teknologier til screening af glasrør både ved ankomst til fabrikken som til det færdige produkt. Systemet indeholder et visuelt inspektionssystem (NoVIS), et system til fortfarende temperaturkontrol, samt et digitalt billedbehandlingssystem, CLEANER, der kan detektere og fjerne urenheder, der er så små som nogle få mikroner, i det færdige glasprodukt. Det fuldt integrerede maskineri til produktionen indeholder udstyr til måling af diameteren af glasrør, tykkelsen af glasset samt måling af temperaturen ved hjælp af infrarøde pyrometre (Pyrometer Annealing control), til fuldstændig kontrol af kvaliteten – motoriserede brændere muliggør nøje kontrol med positionen af brænderne.
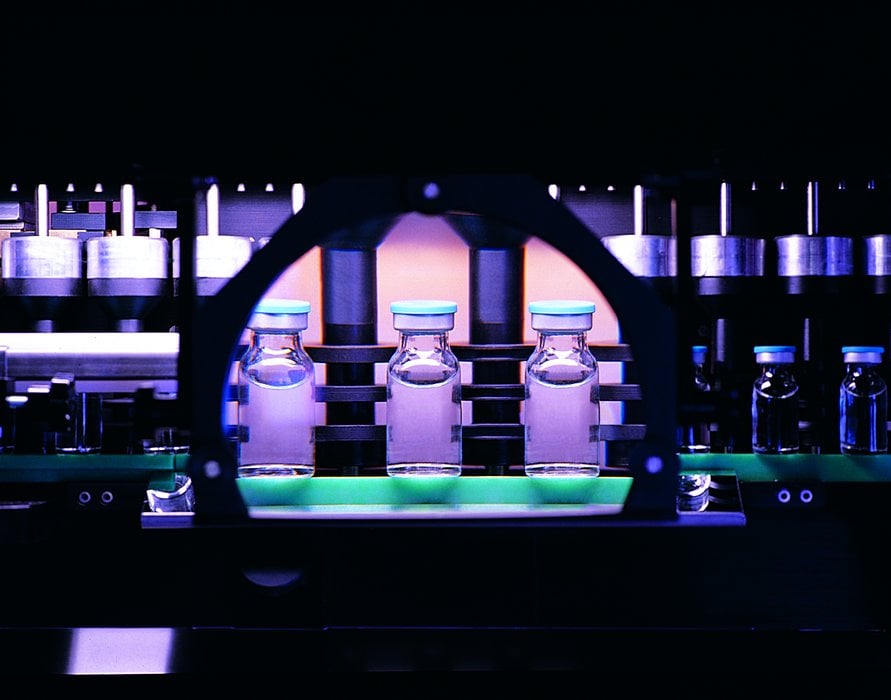
Brugen af dette system har medført en fordel for Stevanato i forhold til andre producenter af hætteglas. Til det avancerede system anvender S.P.A.M.I. Anybus konvertere til forbindelsen mellem kameraer til visuel inspektion og de PLCer, der styrer produktionslinierne.
Stevanato Group blev grundlagt i 1949 som et værksted med kunstindustri i en egn der har stærke traditioner for kunsten at fremstille glas. Stevanato Group er nu en veletableret industriel virksomhed, der fremstiller højteknologiske systemer.
Gruppen omfatter to afdelinger: Glas afdelingen er særligt specialiseret i produktion af fortrinsvis glasrør til emballager til den farmaceutiske industri. Virksomheden har en bred palet af produkter, fra den mest traditionelle emballage som ampuller og hætteglas til de hurtigt voksende produktlinier med hylstre til selvindsprøjtnng og injektionspenne, inklusive sterile klar-til-brug sprøjter
Afdelingen for udvikling, der udgøres af S.P.A.M.I. og Optrel, har fokus på design og produktion af maskiner og udstyr til ændring, visuel inspektion og overvågning af emballage af glasrør. Synergien mellem de to afdelinger sikrer at Stevanato Group har fuld kontrol med hele produktionsforløbet – fra indkøb af råmaterialer helt ned til after-sales support.
S.P.A.M.I.’s produktion er beregnet både til egne virksomheder i gruppen og til salg til andre, eksterne virksomheder. De mekaniske og elektriske løsninger, der er installeret på maskinerne, er designet til at yde den største præcision og de bedste resultater i produktion af glasemballage.
Alle komponenter, der anvendes til at forme det smeltede glas, er installerede og omhyggeligt kontrollerede for at være i stand til at garantere korrekt tolerance i størrelsen af hætteglas, sprøjter, hylstre og ampuller. Komponenterne, der er installeret i maskinerne til bearbejdning af glasset og i de efterfølgende conveyorer er særligt udvalgte for at undgå forurening af emballagen. Processerne er fuldautomatiske, lige fra indføring af det rå glasrør til indpakning af det færdige produkt.
Produktionsforløbet begynder med glasrørene, der ankommer fra underleverandører i længder af ca. 1,5 m og med en passende diameter til størrelsen af det færdige produkt. Glasmaterialet føres ind i roterende formgivningsmaskiner, der er udstyret med adskillige forarbejdningshoveder, der varmes op af brændere. Afhængig af den produktionscyklus, der er valgt i forhold til det produkt, der skal produceres, bliver top og bund af hætteglas, ampul, sprøjter osv. formet på denne måde.
På produktionslinjen er der installeret følgende udstyr:
På den anden side af støbemaskinen er der en conveyor hvor der udføres størrelsesmæssig og kosmetisk inspektion ved hjælp af kameraer for at sikre en gennemgribende kontrol af glasbeholderne.
”Dette er i grunden størrelsesmæssige målinger, der udføres ved at analysere billedet”, forklarer Gobita. ”Da produktet udsættes for belastninger ved udformningen er der også en udglødningsovn, der opvarmer produkterne, samt automatisk emballering af de færdige produkter. Det skal her bemærkes at denne sidste del af produktionsgangen udføres på en sådan måde at kvalitetsniveau og sterilitet, der fordres i farmaceutiske applikationer, er sikret”.
Der er et større antal konkurrenter, der arbejder på internationalt plan, på markedet. ”Vore største konkurrenter er tyske og amerikanske, hvorimod andre virksomheder i Italien er meget mindre end vi er”, forklarer Gobita.
Den værdi, der tilføres af S.P.A.M. skal først og fremmest findes i produktets kvalitet – og det er kvaliteten der har accelereret brugen af produkterne i denne sektor. ”Da vore produkter anvendes i farmaceutiske applikationer er der meget høje krav til kvaliteten, og produkterne skal overholde meget strenge regler og forskrifter. Det medfører at der skal være et stort antal særdeles kvalificerede medarbejdere til kontrolfasen”, fortsætter Gobita.
”Forskellen mellem os og vore nationale konkurrenter skal ses i dette lys. Vor kapacitet indenfor forskning og udvikling er ligeledes en betydelig faktor når farmaceutiske virksomheder udbeder sig prøvematerialer, der afviger fra standard produkter”.
”Vi kan levere produkter udover det standardmæssige fordi vi kan modificere vore systemer. Lige som den mekaniske afdeling, der producerer systemerne i gruppen, kan S.P.A.M.I. ændre og tilpasse disse systemer til at passe til krav fra produktionen”.
”Evnen til at skræddersy systemer er en anden, vigtig værditilvækst som vi kan tilbyde vore kunder. Vi skal her minde om at der er et stort antal standardprodukter i den farmaceutiske industri, som ampuller og hætteglas, som vi ved alt om – men der er også mange specialprodukter, og deres antal er stigende. For størstedelens vedkommende bliver disse specialprodukter udviklet ad hoc. I disse tilfælde er det nødvendigt med en specialmaskine – og i de fleste tilfælde kan en eksisterende maskine modificeres”.
Stevanato Group blev grundlagt i 1949 som et værksted med kunstindustri i en egn der har stærke traditioner for kunsten at fremstille glas. Stevanato Group er nu en veletableret industriel virksomhed, der fremstiller højteknologiske systemer.
Gruppen omfatter to afdelinger: Glas afdelingen er særligt specialiseret i produktion af fortrinsvis glasrør til emballager til den farmaceutiske industri. Virksomheden har en bred palet af produkter, fra den mest traditionelle emballage som ampuller og hætteglas til de hurtigt voksende produktlinier med hylstre til selvindsprøjtnng og injektionspenne, inklusive sterile klar-til-brug sprøjter
Afdelingen for udvikling, der udgøres af S.P.A.M.I. og Optrel, har fokus på design og produktion af maskiner og udstyr til ændring, visuel inspektion og overvågning af emballage af glasrør. Synergien mellem de to afdelinger sikrer at Stevanato Group har fuld kontrol med hele produktionsforløbet – fra indkøb af råmaterialer helt ned til after-sales support.
S.P.A.M.I.’s produktion er beregnet både til egne virksomheder i gruppen og til salg til andre, eksterne virksomheder. De mekaniske og elektriske løsninger, der er installeret på maskinerne, er designet til at yde den største præcision og de bedste resultater i produktion af glasemballage.
Alle komponenter, der anvendes til at forme det smeltede glas, er installerede og omhyggeligt kontrollerede for at være i stand til at garantere korrekt tolerance i størrelsen af hætteglas, sprøjter, hylstre og ampuller. Komponenterne, der er installeret i maskinerne til bearbejdning af glasset og i de efterfølgende conveyorer er særligt udvalgte for at undgå forurening af emballagen. Processerne er fuldautomatiske, lige fra indføring af det rå glasrør til indpakning af det færdige produkt.
Produktionsforløbet begynder med glasrørene, der ankommer fra underleverandører i længder af ca. 1,5 m og med en passende diameter til størrelsen af det færdige produkt. Glasmaterialet føres ind i roterende formgivningsmaskiner, der er udstyret med adskillige forarbejdningshoveder, der varmes op af brændere. Afhængig af den produktionscyklus, der er valgt i forhold til det produkt, der skal produceres, bliver top og bund af hætteglas, ampul, sprøjter osv. formet på denne måde.
På produktionslinjen er der installeret følgende udstyr:
På den anden side af støbemaskinen er der en conveyor hvor der udføres størrelsesmæssig og kosmetisk inspektion ved hjælp af kameraer for at sikre en gennemgribende kontrol af glasbeholderne.
”Dette er i grunden størrelsesmæssige målinger, der udføres ved at analysere billedet”, forklarer Gobita. ”Da produktet udsættes for belastninger ved udformningen er der også en udglødningsovn, der opvarmer produkterne, samt automatisk emballering af de færdige produkter. Det skal her bemærkes at denne sidste del af produktionsgangen udføres på en sådan måde at kvalitetsniveau og sterilitet, der fordres i farmaceutiske applikationer, er sikret”.
Der er et større antal konkurrenter, der arbejder på internationalt plan, på markedet. ”Vore største konkurrenter er tyske og amerikanske, hvorimod andre virksomheder i Italien er meget mindre end vi er”, forklarer Gobita.
Den værdi, der tilføres af S.P.A.M. skal først og fremmest findes i produktets kvalitet – og det er kvaliteten der har accelereret brugen af produkterne i denne sektor. ”Da vore produkter anvendes i farmaceutiske applikationer er der meget høje krav til kvaliteten, og produkterne skal overholde meget strenge regler og forskrifter. Det medfører at der skal være et stort antal særdeles kvalificerede medarbejdere til kontrolfasen”, fortsætter Gobita.
”Forskellen mellem os og vore nationale konkurrenter skal ses i dette lys. Vor kapacitet indenfor forskning og udvikling er ligeledes en betydelig faktor når farmaceutiske virksomheder udbeder sig prøvematerialer, der afviger fra standard produkter”.
”Vi kan levere produkter udover det standardmæssige fordi vi kan modificere vore systemer. Lige som den mekaniske afdeling, der producerer systemerne i gruppen, kan S.P.A.M.I. ændre og tilpasse disse systemer til at passe til krav fra produktionen”.
”Evnen til at skræddersy systemer er en anden, vigtig værditilvækst som vi kan tilbyde vore kunder. Vi skal her minde om at der er et stort antal standardprodukter i den farmaceutiske industri, som ampuller og hætteglas, som vi ved alt om – men der er også mange specialprodukter, og deres antal er stigende. For størstedelens vedkommende bliver disse specialprodukter udviklet ad hoc. I disse tilfælde er det nødvendigt med en specialmaskine – og i de fleste tilfælde kan en eksisterende maskine modificeres”.
Positivt samarbejde med HMS
Samarbejdet med HMS kom i stand for at løse et specifikt problem med kommunikation.
Den mekaniske afdeling havde udviklet en applikation, der skulle udføre en serie af kvalitetskontroller af produkter, der var baseret på maskinel visions teknologi: Cognex kameraer skulle forbindes til Siemens PLCer”.
”Vi havde derfor behov for at få kameraerne med Ethernet interface til at kommunikere med PLCer med Profibus protokol”, forklarer Gobita. ”Efter omhyggelige undersøgelser og via EFA Automation, der er eneforhandlere i Italien af HMS gateway løsninger, fandt vi nogle Anybus enheder, der gjorde os i stand til at løse problemet med kommunikationen mellem vort udstyr”.
Andre potentielle leverandører var med i overvejelserne på dette tidspunkt, men HMS var det eneste firma der kunne tilbyde et bredt spektrum at protokol omformere.
”Den brede tilgang var afgørende for vort valg da vore forskellige applikationer ofte varierede meget. I begyndelsen skulle vi for eksempel kunne administrere Profibus protokollen da det var denne der blev anvendt af Siemens PLCerne – men vor virksomhed brugte normalt også andre, programmerbare kontrollere fra andre leverandører. Så det var afgørende for os at have et bredt udvalg af produkter”.
Det første HMS produkt, der kom i anvendelse, var en enhed fra Anybus konverterne, der omformer Profibus til Modbus on Ethernet: Anybus X-gateway.
Der kan installeres mere end én Anybus omformer på hver produktionslinie. ”Ind til nu har vi anvendt flere konvertere fordi applikationen har været brugt i forskellige systemer”, fortæller Gobita. ”Intelligente kameraer anvendes til at undersøge de forskellige kvalitetskriterier for produkterne, og de skal installeres på adskillige lokationer i systemet. I grunden er det ikke en skræddersyet HMS konverter applikation men en applikation der er blevet standard for os”.
“Vi er meget tilfredse med vort valg. HMS Anybus produkter er meget pålidelige, funktionelle og enkle at bruge, sammenlignet med tilsvarende enheder som vi har testet. Alle ved at selv om det er nemt at finde komplekse løsninger er det straks meget vanskeligere at finde ting, der er nemme og enkle at anvende.
”Vi har ikke haft nogen som helst problemer, og den måde som tingene har udviklet sig på, skyldes også dette. I fremtiden vil vi ligeledes bruge HMS Anybus konvertere på andre linier hvor de selvfølgelig vil være tæt knyttet til vore kontrol systemer via kameraer”.
”Og da branchens standarder kræver stadig mindre tolerancer er det uafvendeligt at kontrol med fjernbetjente kameraer vil blive mere og mere almindelig”, konkluderer Gobita.
Samarbejdet med HMS kom i stand for at løse et specifikt problem med kommunikation.
Den mekaniske afdeling havde udviklet en applikation, der skulle udføre en serie af kvalitetskontroller af produkter, der var baseret på maskinel visions teknologi: Cognex kameraer skulle forbindes til Siemens PLCer”.
”Vi havde derfor behov for at få kameraerne med Ethernet interface til at kommunikere med PLCer med Profibus protokol”, forklarer Gobita. ”Efter omhyggelige undersøgelser og via EFA Automation, der er eneforhandlere i Italien af HMS gateway løsninger, fandt vi nogle Anybus enheder, der gjorde os i stand til at løse problemet med kommunikationen mellem vort udstyr”.
Andre potentielle leverandører var med i overvejelserne på dette tidspunkt, men HMS var det eneste firma der kunne tilbyde et bredt spektrum at protokol omformere.
”Den brede tilgang var afgørende for vort valg da vore forskellige applikationer ofte varierede meget. I begyndelsen skulle vi for eksempel kunne administrere Profibus protokollen da det var denne der blev anvendt af Siemens PLCerne – men vor virksomhed brugte normalt også andre, programmerbare kontrollere fra andre leverandører. Så det var afgørende for os at have et bredt udvalg af produkter”.
Det første HMS produkt, der kom i anvendelse, var en enhed fra Anybus konverterne, der omformer Profibus til Modbus on Ethernet: Anybus X-gateway.
Der kan installeres mere end én Anybus omformer på hver produktionslinie. ”Ind til nu har vi anvendt flere konvertere fordi applikationen har været brugt i forskellige systemer”, fortæller Gobita. ”Intelligente kameraer anvendes til at undersøge de forskellige kvalitetskriterier for produkterne, og de skal installeres på adskillige lokationer i systemet. I grunden er det ikke en skræddersyet HMS konverter applikation men en applikation der er blevet standard for os”.
“Vi er meget tilfredse med vort valg. HMS Anybus produkter er meget pålidelige, funktionelle og enkle at bruge, sammenlignet med tilsvarende enheder som vi har testet. Alle ved at selv om det er nemt at finde komplekse løsninger er det straks meget vanskeligere at finde ting, der er nemme og enkle at anvende.
”Vi har ikke haft nogen som helst problemer, og den måde som tingene har udviklet sig på, skyldes også dette. I fremtiden vil vi ligeledes bruge HMS Anybus konvertere på andre linier hvor de selvfølgelig vil være tæt knyttet til vore kontrol systemer via kameraer”.
”Og da branchens standarder kræver stadig mindre tolerancer er det uafvendeligt at kontrol med fjernbetjente kameraer vil blive mere og mere almindelig”, konkluderer Gobita.